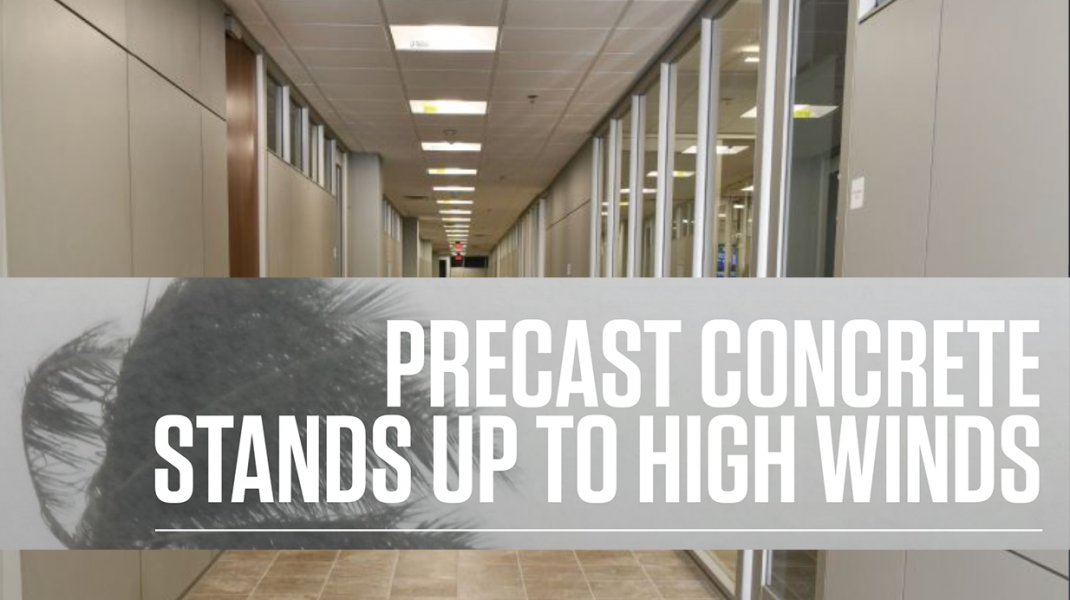
Precast Concrete Buildings Survive Direct Hits from Hurricanes
Hurricanes Laura and Delta were no match for these precast buildings, which combine precast concrete and steel for a nearly impregnable facade.
A pair of precast concrete projects in Louisiana withstood the wrath of two powerful hurricanes as structures around them were demolished. Bob Pool, executive vice president of Alfred Miller Companies (AMC), a design-build contractor that also manufactures precast concrete components, documented the after-effects of Hurricanes Laura and Delta on the control room, maintenance shop, and warehouse (CMW) building of Cameron LNG, a liquified natural gas facility in Hackberry, La., and on the Cameron Parish School District (CPSD) Warehouses in Creole, La.
“This year our area had direct hits from two major hurricanes, six weeks apart,” says Pool. “Cameron LNG’s CMW building in Hackberry was hit by 150-mile-per-hour sustained winds and 200-mile-per-hour gusts during Hurricane Laura. The only damage [to the CMW building], a laboratory and hazardous-waste storage facility, was to the fabric parking canopy, which was designed to tear away in a hurricane.” Pool says several pre-engineered metal buildings (PEMBs) in the same area sustained significant damage.
“They are literally the only buildings still standing within a 10-mile radius of Creole.”
The school district warehouses are located a mile from the coast, exactly where Hurricane Delta made landfall, he says. Both structures are pre-engineered metal buildings with precast concrete walls and standing-seam metal roofs. “They are literally the only buildings still standing within a 10-mile radius of Creole,” Pool says.

AMC shop-applied more than 2 million square feet of lightweight cementitious fireproofing and completed field block-outs, plus equipment supports (shotcrete) totaling more than 2.4 million square feet. The project is the largest fireproofing job in U.S. construction history, says Pool. The company also provided four miles of precast concrete trenches for LNG and stormwater containment, and two miles of precast concrete underground electrical duct banks and manholes.
Surviving Spills and Storm Surge
For the CPSD Warehouses, the biggest risk was being in the direct path of both the hurricane eyewall and storm surge, says Philip Miller, president of AMC. “The building is literally within sight of the Gulf of Mexico,” Miller says. “This is exactly what happened during Hurricane Laura and Hurricane Delta, which had a 17-foot storm surge.”
The new structures replace a previous warehouse that was destroyed by Hurricane Rita. Because they’re located directly on the beach highway, they are elevated to minimize future risk, Miller says. Their purpose is to store frozen and refrigerated food and dry goods for school cafeterias throughout Cameron Parish. This design-build, public-bid project was designed by Brossett Architect in Lake Charles, La.

The Cameron LNG building is built literally in the shadow of the giant tanks containing liquefied natural gas. “These tanks are 300 feet in diameter and 200 feet high and hold more than a ship load of LNG apiece,” Miller says. “The greatest risk is blast exposure from a hydrocarbon vapor cloud that could result from an unintentional LNG spill.”
The building is a total–precast concrete project “because it provides the greatest value,” he says. “We make total–precast competitive with PEMBs or steel-frame buildings by integrating large amounts of MEP [mechanical, electrical, and plumbing] and sprinkler-system [components] into the precast before shipping it to the construction site. We even apply the roof insulation and roof membrane before shipping the roof panels.”
Design and Construction Challenges
The biggest design challenge in the CPSD project was to build a ramp up to the desired 12-ft elevation for deliveries by tractor-trailer trucks. “Another significant challenge was the relatively remote location,” says Miller. “The nearest concrete batch plant was over an hour away.”
The Cameron LNG building presented even bigger challenges. “The footprint was part of the impoundment basin for the LNG tanks,” he says. “The basin exists to contain millions of gallons of LNG in the event of a catastrophic failure of the piping or the tanks themselves.” LNG, he adds, is a liquid that is -270°F and boils off upon exposure to the atmosphere to a vapor cloud of pure natural gas.
In addition, the building was part of a much larger, $10 billion project to convert an existing LNG Import Facility into an Export Facility. Because the original facility was “live” — full of hydrocarbons and in operation — the area was considered a brownfield, says Miller.
Construction took place during an extremely wet year, when Hurricane Harvey dumped 60 in. of rain on some areas in two days, he says. The building site needed to be raised by 6 ft, but the earthwork was significantly delayed by constant rain. At the start of construction, the schedule was already six months behind.
To overcome these issues, AMC devised a method of precasting the entire foundation of the building. “We drove the precast piles so that they stuck out of the ground by six feet and installed all of the pile caps for the building columns and perimeter grade beams for the walls at that elevation.”
This innovation recovered four months [that had been lost from] our schedule.”
Once the piles, caps, and grade beams were installed, the company installed 20,000 cubic yards of flowable fill, specifically lean concrete, to bring the entire site up to grade. “This innovation recovered four months [that had been lost from] our schedule,” he says. Lean concrete is a mixture in which the amount of cement is lower than the amount of liquid in the strata, which provides a uniform and level surface underneath foundations.
The major logistical challenge for the Cameron LNG building was that no staging area was available. “Every component from the foundation to the roof had to be delivered to the site just in time and directly to the crane hook,” says Miller. “This all had to be executed in a live operating hydrocarbon facility.”
View this Main Feature article in the Precast Concrete Institute’s Summer 2021 ASCENT publication here.