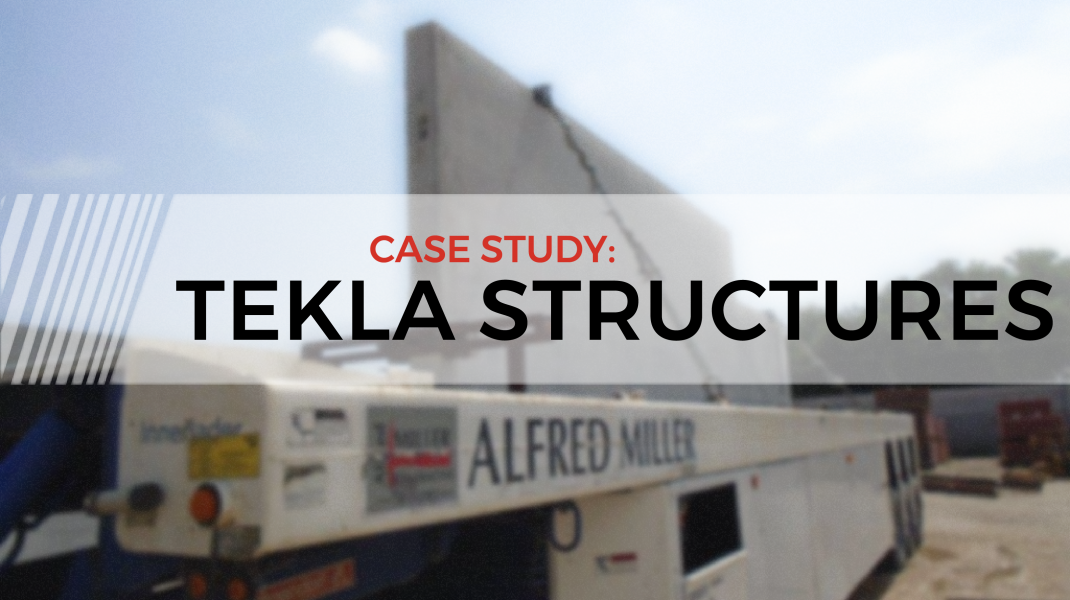
Case Study: How We Engineered A Better Precast Floor Slab
Innovation and flexibility are core philosophies for how we work. We approach every project as its own unique challenge and an opportunity to innovate and do better, regardless of what the industry standard is. The following case study exemplifies how we innovate, work, and engineered a better structural floor slab and precast manhole chamber using industry-leading engineering software applications, saving our industrial customer money.
Better Engineering – The Structural Floor Slab Design
In early 2015, our team won a bid to construct a large blast rated maintenance warehouse building which also housed the control room for a new $10 Billion Liquefied Natural Gas plant. The precast warehouse structure included a structural concrete floor slab.
At first, the engineering design seemed straightforward. The structural floor slab (200ft x 325ft x 12” thick) is supported by 401 piles below. The slab/pile combination needed to support heavy equipment loading in certain areas, including storage racks, jib cranes, and even HS20 truck loading.
Our Engineering Technology Manager, Rebekah Morlock, began her analysis via a traditional approach, utilizing manual techniques and empirical evidence to optimize the design. “Unfortunately, the analysis proved impossible to perform effectively. I couldn’t get a good feel for the pile loads and overloads to allow me to optimize the number and placement of them within the very large space.”
So, Morlock turned to our upper management with a solution: Trimble’s Tekla Structural Designer. Tekla Structural Designer is an engineering solution for analyzing and designing concrete and steel systems of all scopes and scales with sophisticated modeling, analysis, and design tools. The Building Information Modeling (BIM) software enables the creation and management of accurately detailed, highly constructable 3D structural models regardless of material or structural complexity.
Morlock was able to model the structural floor slab project using a finite element approach to analyze a stronger, more cost effective slab concept, immediately saving $70,000 by reducing the amount of reinforcing required and optimizing the location of the piles below as compared to her manually prepared concept. Morlock used the solution to model five interconnected slabs to create the whole slab in about 30 minutes.
She says, “The software is smart enough to know that even if I break up the slabs to simplify construction and support multiple pours, that all elements will carry loads as one system.” She continued, “Ultimately, we saved $126,000 in reinforcement that would have been required had we gone with the empirical approach. Ever since this first project, Tekla Structural Designer has become a mainstay here at Alfred Miller Contracting.”
Ultimately, we saved $126,000 in reinforcement that would have been required had we gone with the empirical approach. Ever since this first project, Tekla Structural Designer has become a mainstay here at Alfred Miller Contracting.
She adds, “Our company is unique in that we can’t just design to the cheapest material cost; we also have to look at production cost of the precast and schedule, as sometimes, schedule is more important than cost.”
Better Design – A Precast Manhole Chamber
Soon after completing the design of the maintenance warehouse, Alfred Miller Contracting was tasked to engineer a 98,000 lbs, 17’-4” x 17’-4” by 14’-0” tall precast manhole chamber for another process within the same industrial plant.
Morlock says, “Early on, we analyzed the manhole project by hand for in-place construction. When we shifted from a cast-in-place product to a precast prefabricated solution, we realized that we needed to evaluate the system for three conditions: in service, lifting, and transportation. However, we had no precedent for this type of analysis.”
With Tekla Structural Designer, Rebekah was able to design a solution for all three scenarios. “There is no other way we could have designed this system within the scope defined by the owner,” she adds.
Her design worked beyond expectations. The manhole chamber was fabricated at Alfred Miller Contracting’s headquarters, lifted by two cranes onto a truck, and delivered to the site on schedule. Since installation, the owner has not noted any structural problems.
Since those early days, Alfred Miller Contracting continues to utilize leading-edge structural design solutions to execute better practices in precast building construction. Morlock concludes, “Our customers, particularly those in the industrial sector, are exacting and time-driven. They need for us to have the flexibility to change and still maintain hard deadlines.”
Read the full case study developed in collaboration with Trimble here.
ABOUT ALFRED MILLER CONTRACTING:
A nationwide contractor based in Lake Charles, Louisiana, Alfred Miller Contracting has created innovative solutions for Industrial and Commercial construction projects, processes, and operations throughout North America for 70 years.
A recognized authority in fireproofing, buildings, and precast, Alfred Miller Contracting has earned a distinctive reputation in the petrochemical industry’s Downstream vertical, as the company’s notable history of innovation has literally paralleled its growth since the 1940s.